Only 3D printing can get the Navy’s submarine plan back on track, admiral says
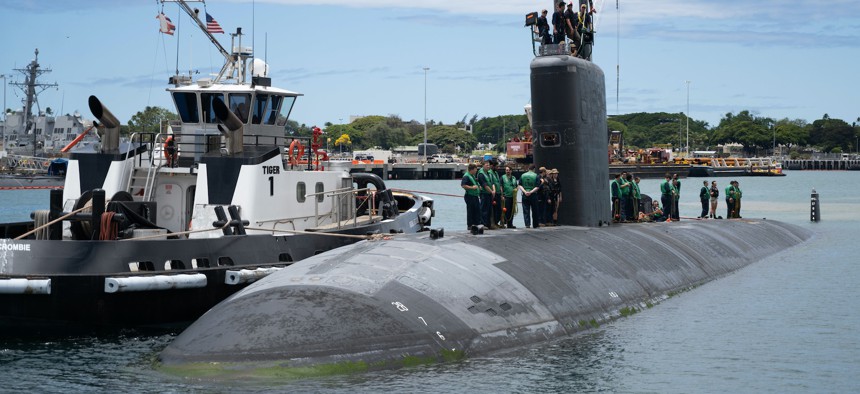
The Los Angeles-class fast-attack submarine USS Topeka (SSN 754) pulls into port following a routine underway, June 16, 2022. U.S. Navy / Mass Communication Specialist 3rd Class Molly Crawford
U.S. cannot build and support the subs it needs “without going to additive manufacturing.”
The U.S. Navy must 3D-print more parts if it is to build three submarines per year, a top program manager said Wednesday.
Rear Adm. Jonathan Rucker, the Navy’s lead buyer for attack submarines, said additive manufacturing has become essential for meeting construction schedules—and then keeping those new subs operating.
“Absolutely we need to have additive manufacturing,” Rucker told lawmakers during a House Armed Services Subcommittee hearing. “If you look across components on the ships—forgings, castings, fittings, valves, fasteners—we cannot meet the demand to be able to support building the submarines we need, as well as supporting sustainment, without going to additive manufacturing.”
The first 3D-printed parts are already starting to be installed, said Rucker, who led the Navy’s Columbia-class ballistic-missile submarine program before taking his current job last year.
“Already this year, we put the first part out of manufacturing on a ballistic missile submarine to ensure they could make their schedule. The second part we had, a critical valve that's needed, that valve was going to be two years late. We've reverse-engineered it; it is being [3D printed] as we speak. They will make it on that submarine by January to support its schedule,” he said.
Rucker is not the first top Navy official to urge greater use of 3D printing for subs. Matt Sermon, executive director of the strategic submarines program executive office, said as much in March. But Rucker’s call comes as the service continues to struggle to obtain parts in a timely manner, and as sub-building shipyards juggle workers and resources in a bid to prevent further production delays. And the Navy isn’t just aiming to prevent delays; it wants to increase production to one Columbia-class and two Virginia-class submarines each year.
To do that, the service is asking lawmakers for more authorities and funding. On Oct. 20, the White House proposed that Congress authorize $3.4 billion in supplemental funding as part of a much larger package that also supports aid for Ukraine and Gaza. About $2 billion would go to boost the submarine industrial base, including about 15 percent for developing technologies such as additive manufacturing and the parts testing and inspection, Rucker said.
“That supplemental continues to jumpstart when we did the study back a couple years ago, that was one area. We underestimated the opportunity that was there,” he said.
Rep. Jack Bergman, R-Mich., raised concerns about integration and making sure everyone was collaborating, from senior defense officials to the workers who are actually building the boats.
“What I'm worried about is, the future, as we design and build things…what do we put in place, if anything, even if it's just a straw man right now, to ensure that as we get into this, the [information] sharing occurs,” Bergman said. “It's one thing for the defense ministers to get together. It's another thing for the people doing all the welding to get together.”
The Navy’s additive manufacturing effort is also part of the trilateral agreement between Australia, the United Kingdom, and the United States, or AUKUS. Rucker reassured the congressman, noting that his office, the program executive office for attack submarines, is in the same building as the AUKUS integration office and that the Navy stood up an additive manufacturing consortium and center of excellence in Danville, Virginia.
“One of the Australian companies, it's called AML.3D, is part of that consortium. They're already trading and coordinating on how they go about the technical data packages to improve how we actually do additive manufacturing, leveraging the lessons learned they have,” Rucker said.